What is Inventory Management?
Inventory Management is a method to ensure parts are tracked from the time they are manufactured until they are delivered or installed. Parts must be traceable through every step and movement they make. The status of location and quantity of each part must be available at any moment so all stakeholders can use the most up to date information to make informed decisions. At China Stainless Steel Screws, we know how important it is that you have the most accurate information possible. With over 72 years of experience and over 70,000 sq. ft. of warehouse space, we have the expertise to implement many different types of inventory management systems, depending on your needs. Contact us today to learn more about our fastener inventory management services.
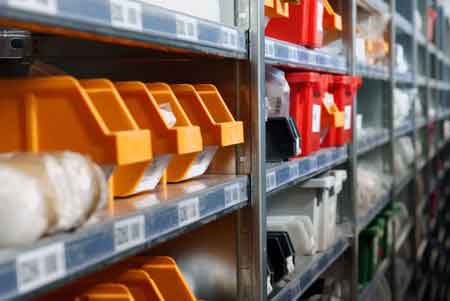
China Stainless Steel Screws Provides Professional, Efficient Inventory Management Programs
China Stainless Steel Screws knows that flexibility matters to our customers. Our inventory management solutions provide flexibility and peace of mind knowing your parts will always be ready for you in our 75,000 square foot warehouse. Whether it’s one part or several hundred, China Stainless Steel Screws takes into account every consideration when it comes to managing our customer’s’ inventory. Whether it’s producing competitive parts on the right type of machine, providing preproduction samples, inspecting each and every dimension of each and every lot manufactured or received, packaging for protection, or simply holding product in stock for release when you need it --China Stainless Steel Screws manages your inventory for you.
Cost Savings
We recognize that cost containment is a big part of our job. Instead of using your valuable time to worry if parts will show up on time, China Stainless Steel Screws can step in and assume the role of inventory manager and allow you to focus your energy on other projects. No more spending time deciding when to order or how many to order. China Stainless Steel Screws will keep track each parts usage and inventory and let you know when a re-order will make sense. In addition to saving you money on the piece price for your parts, we can save you valuable time and resources by freeing you up to handle more important business tasks.
When we manufacture or source parts for you, we utilize the most effective and competitive machinery. With that in mind, we regularly visit & audit our suppliers, both domestic and overseas. Our inventory management solutions allow you to get better pricing through volume discounts by ordering your estimated annual usage and allowing China Stainless Steel Screws to manage your inventory in our warehouse.
Inventory for Release
There are many different inventory programs available through China Stainless Steel Screws. Each program can be tailored for specific customer requirements and results in the following benefits:
- Reduced inventory on hand
- Less handling of parts, less paperwork lowering labor and administrative costs.
- You do not pay for parts until they are in your hands, increasing your cash flow.
- Increased Inventory turns
- Less warehouse space required
- Backup product available for production spikes.
We look at your annual use estimates and work with you to ensure inventory is available when you need it but not on your books or balance sheet until then. We make sure you are only responsible for inventory which you commit to. We manage the cost, storage, delivery so you can focus on where you excel -- your product line. We are confident one of our inventory management programs will be a fit for you!
Stock and Release
China Stainless Steel Screws will stock and release your parts based on your EAU. By purchasing your EAU all at once, we can provide a lower price via volume discounts. We will keep your parts in our 70,000 sq ft. warehouse and ship when you release. Each lot is thoroughly inspected before they go on the shelf. This will keep your production lines running and keep you from shutting down due to part availability or defective parts. By reducing inventory in your facility and maximizing inventory turns, China Stainless Steel Screws allows you to avoid spending time and resources on managing a large number of parts.
Just in Time (JIT)
Just in time inventory management is a solution where parts don’t show up to your factory until the day they are needed for a build. We will work with you to create a delivery schedule to ensure you get your custom components when you need them. This eliminates the need for warehouse space saving you money on space, manpower, administration, and all other related overhead. It also allows your production to be more efficient and prevent waste.
Consignment
Consignment is an inventory agreement that allows the customer to keep stock in inventory at their facility while the supplier maintains ownership of the inventory. The customer will only pay for the parts as they are used. The clear benefit with this system is the cost savings for you, the customer. You don’t pay for the parts until you have used them. The tradeoff is needing the warehouse space to store the inventory and the associated costs. China Stainless Steel Screws will work with you to consign product.
Automatic Replenishment Programs
An automatic replenishment program, which can also be called a stocking agreement, is a program where the supplier places a new order for parts once an agreed upon threshold has been met. China Stainless Steel Screws will track your part usage and based on your estimated annual usage as well as what we have in stock; we will place a new order for parts when that threshold is met. The threshold can be a certain stock level or based on estimated lead time of parts. The benefit of this is we will take the time to track stock and usage of all your parts and place orders when needed so we don’t run out of parts while also making sure we don’t overstock. We will make sure you always have parts available to you.
Barcoding, Labeling, and Lot Traceability
To help you streamline your inventory management operations, China Stainless Steel Screws will work with you on putting together a barcoding and labeling program so you can accurately and quickly trace lots and find order information. Barcoding and labeling eases the receiving process and increases quality by eliminating a potential source of human error. Parts will always go to the correct location, so they are never lost causing a slowdown in production.
Lots are a group of parts that are made at the same time in the production run using the same materials. Having the ability to trace lots allows you to track parts in your facility through use in production. Each lot is given a lot number and all the parts produced at the same time are grouped under this number. With this lot traceability, you can track what materials are used, when they are used, and in what products they are used. If there is a problem with a part, lot traceability makes it extremely easy to identify the problem location.
China Stainless Steel Screws has a multitude of solutions to fill a variety of needs. We are confident that we can become a valued partner or yours. If you were out of product any time in the last few years due to a supplier not having parts available, then give us a call to see how one of our inventory management systems can benefit you.