Why Choose Nylon Fasteners?
Nylon often replaces bronze, brass, steel, aluminum and several other metals as well as several types of plastics, rubber and wood. It’s one of the most popular polymers used for industrial parts because they can be precisely machined to the tightest tolerances. It is a relatively low-cost plastic that is perfect for parts that require high compressive strength. Although it is cheaper than other plastics such as PEEK and PTFE, nylon is a strong material that creates high-quality parts.
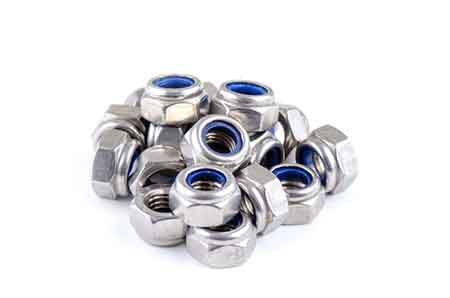
Nylon Fastener Manufacturing
Nylon parts are manufactured using a variety of plastics. For example, Acetal may be used to bolster durability while minimizing water absorption. Polyvinyl chloride or PVC is used to enhance the hardware’s ability to resist the elements. Polypropylene, on the other hand, helps increase both durability and strength. Types of manufacturing processes for nylon can be CNC machining, automatic screw machining, and molding. These types of nylon fastener are often used in electronics, telecommunications, computers and automotive systems.
*Available in inch and metric sizes.
Benefits of Nylon Machined Parts:
- High amount of insulation and resistance to corrosion, impact, and abrasion.
- Nylon is lighter, stronger and offers high wear resistance, providing longer-wearing machined parts that require less maintenance than metal.
- Nylon machining is ideal for the production of fire-resistant items since it melts NOT burn.
- High tensile strength and elasticity modulus.
Types of Nylon:
- Acetal enhances durability and minimizes water absorption
- Polyvinyl chloride (PVC) helps nylon resist natural elements such as rain and sunlight
- Polycarbonate enables nylon fasteners to withstand heat and electricity
- Polypropylene amplifies the positive effects other materials have on nylon
- Nylon 6/6 provides durability, tensile strength, and resistance to creep, particularly in the high temperature range.
Types of components made with nylon are:
- Fittings
- Bushings
- Rivets
- Washers
- Threaded components